After testing a FLIR camera that attaches to a phone, I would say it was worth the $200 investment. I am in a 4800 sqft house that was built in 1858 and there are many areas where cold air infiltration occurs. The FLIR camera made it possible to easily locate where the cold air was entering the house or where heat is escaping. I also use the FLIR camera to inspect electrical wiring and measure the temperature of the woodstove and flue.
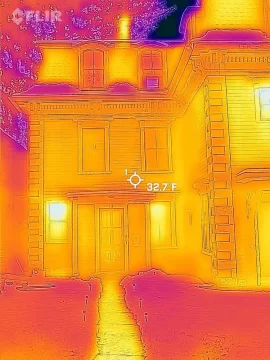
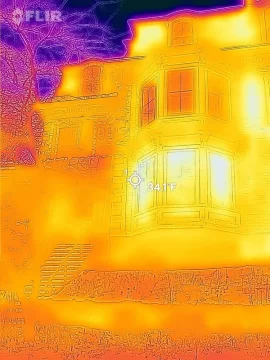
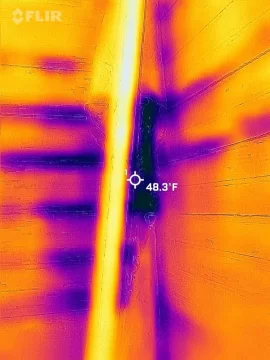
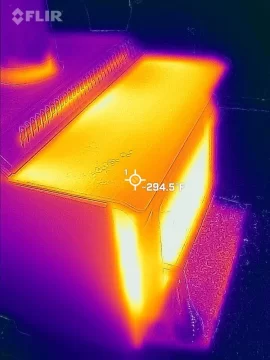
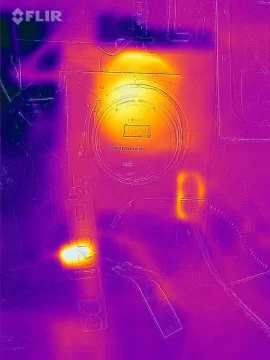
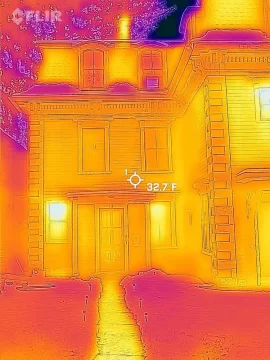
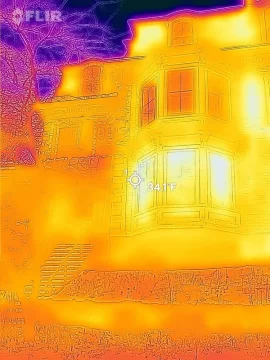
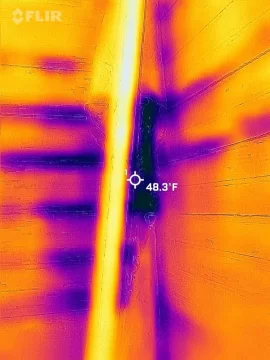
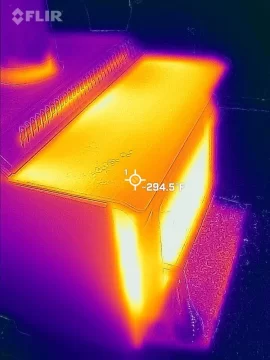
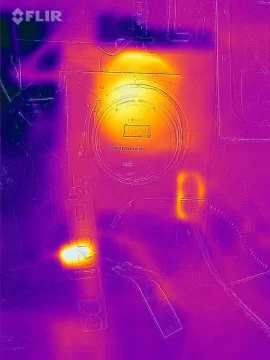