I would like to add an additional pump to my system to increase flow when I get near the end of storage charging. I would control it with an aqua-stat that would activate the pump at a desired supply temp to increase the gpm.
I am thinking about placing a T in the supply line near the boiler and back in before the storage tank.
I need some advice on where to place the T and if there are any drawbacks or concerns.
Some of my concerns are location of new pipe in relation to;
1. Air separator
2. Bypass for Danfoss
I have included a picture with my initial choice.
gg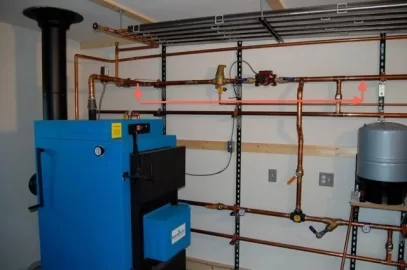
I am thinking about placing a T in the supply line near the boiler and back in before the storage tank.
I need some advice on where to place the T and if there are any drawbacks or concerns.
Some of my concerns are location of new pipe in relation to;
1. Air separator
2. Bypass for Danfoss
I have included a picture with my initial choice.
gg
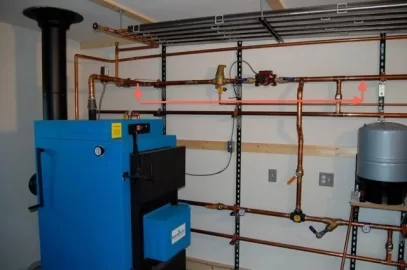