Hello all and thanks for all of the helpful info you have created on this forum.
I am in the process of removing an FMI 24GC zero clearance fireplace that was original to the home when it was built in 1988. It has a wood framed / wood sided exterior chase on our 2 story home in which the fireplace is on the first floor. The flue is currently a 12" outer 8" inner double walled air cooled device that I am 99% sure I cannot use for my wood stove...
I played with the idea of using an insulated 6" ID flue liner to increase the heat capacity inside of my existing ZC flue, but I have decided against that, unless you all think that is OK to do? I doubt it though
I have a 2017 Hearthstone Mansfield 8012 soapstone stove that I installed in my previous home and then removed and took with us when we sold the home which was in Oakhurst, CA. I love that stove and have really enjoyed it.
So he is my plan:
1: Remove old ZC stove (DONE)
2: Remove old flue
3: Frame an alcove protruding from the wall about 10-12" to allow the stove to sit inside the old ZC framing but also be flush at the front. I don't really want it sticking half way into the room. The first floor is only about 900 sqft and I don't think I will loose much heat by having it in an alcove. The alcove will allow for a small mantle as well and we like the style of it.
a) my current framing opening is 53" wide, 26" deep and I plan to move the header up to 60" height for a higher mantle.
b) Hearthstone allows for 10" clearance per side and 10" in the rear with the blower and shield. (which I have) and 18" above the stove to the alcove ceiling.
c) the minimum size my alcove can be is 48" wide 46" high and 34" deep. Once I add all the heat sheilding I will be at that width and depth but probably about 60" high.
d) the ZC had electrical and gas already ran to it. I want to run the gas line to the rear of the alcove and cap it off, for a possible future gas stove if I ever have to use one.
e) I will run the electric outlet to the rear of the alcove for my blower, adding a wall switch to operate it.
f) I plan to put an outside air supply in the rear of the alcove also, I haven't used that for my stove previously but would like to now.
4: I plan to use metal hat-track channel (horizontally on the studs for air gap) durarock, and brick vaneer to achieve the NFPA 211 non-combustable clearances allowed my Hearthstone. (more questions on that process in future posts!)
- not sure if I should add some roxsul insulation between the studs or not.
5:For the hearth I plan to use durarock and solid brick installed over the 3/4" plywood subfloor.
6: Replacing the existing flue with Class A flue to extend from the stove pipe up through the chase aprox. 22' and install a new or modify the existing chase cap for the smaller size flue. There are 2 fire stops that exist in the chase and I am not sure how I will modify those for the smaller flue
I am sure I am forgetting a few things but that is my rough plan, I have been reading and reading for months to research all of this and I know I will have more questions soon. Feel free to add your thoughts or input and concerns if you have any!
The photos are my ZC removal and the current blank slate that I am in, my Hearthstone Mansfield and an internet picture of the basic idea that I am going for plus some specs on my stove.
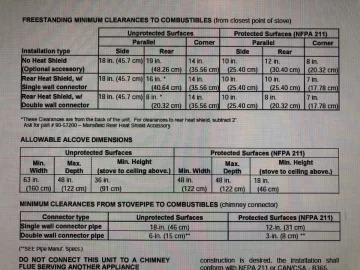
I am in the process of removing an FMI 24GC zero clearance fireplace that was original to the home when it was built in 1988. It has a wood framed / wood sided exterior chase on our 2 story home in which the fireplace is on the first floor. The flue is currently a 12" outer 8" inner double walled air cooled device that I am 99% sure I cannot use for my wood stove...
I played with the idea of using an insulated 6" ID flue liner to increase the heat capacity inside of my existing ZC flue, but I have decided against that, unless you all think that is OK to do? I doubt it though
I have a 2017 Hearthstone Mansfield 8012 soapstone stove that I installed in my previous home and then removed and took with us when we sold the home which was in Oakhurst, CA. I love that stove and have really enjoyed it.
So he is my plan:
1: Remove old ZC stove (DONE)
2: Remove old flue
3: Frame an alcove protruding from the wall about 10-12" to allow the stove to sit inside the old ZC framing but also be flush at the front. I don't really want it sticking half way into the room. The first floor is only about 900 sqft and I don't think I will loose much heat by having it in an alcove. The alcove will allow for a small mantle as well and we like the style of it.
a) my current framing opening is 53" wide, 26" deep and I plan to move the header up to 60" height for a higher mantle.
b) Hearthstone allows for 10" clearance per side and 10" in the rear with the blower and shield. (which I have) and 18" above the stove to the alcove ceiling.
c) the minimum size my alcove can be is 48" wide 46" high and 34" deep. Once I add all the heat sheilding I will be at that width and depth but probably about 60" high.
d) the ZC had electrical and gas already ran to it. I want to run the gas line to the rear of the alcove and cap it off, for a possible future gas stove if I ever have to use one.
e) I will run the electric outlet to the rear of the alcove for my blower, adding a wall switch to operate it.
f) I plan to put an outside air supply in the rear of the alcove also, I haven't used that for my stove previously but would like to now.
4: I plan to use metal hat-track channel (horizontally on the studs for air gap) durarock, and brick vaneer to achieve the NFPA 211 non-combustable clearances allowed my Hearthstone. (more questions on that process in future posts!)
- not sure if I should add some roxsul insulation between the studs or not.
5:For the hearth I plan to use durarock and solid brick installed over the 3/4" plywood subfloor.
6: Replacing the existing flue with Class A flue to extend from the stove pipe up through the chase aprox. 22' and install a new or modify the existing chase cap for the smaller size flue. There are 2 fire stops that exist in the chase and I am not sure how I will modify those for the smaller flue
I am sure I am forgetting a few things but that is my rough plan, I have been reading and reading for months to research all of this and I know I will have more questions soon. Feel free to add your thoughts or input and concerns if you have any!
The photos are my ZC removal and the current blank slate that I am in, my Hearthstone Mansfield and an internet picture of the basic idea that I am going for plus some specs on my stove.
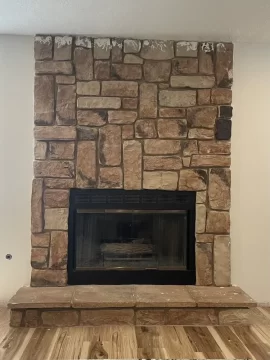

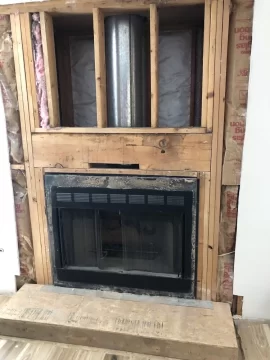
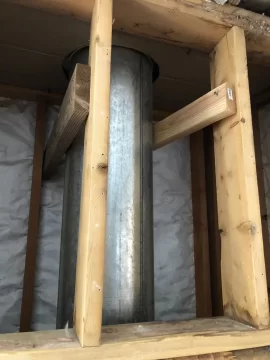
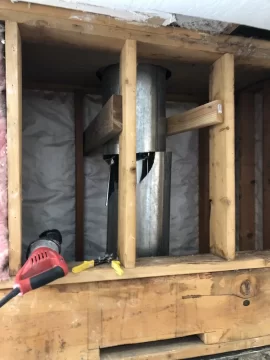
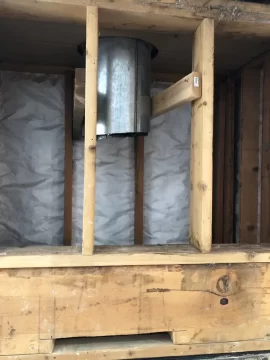
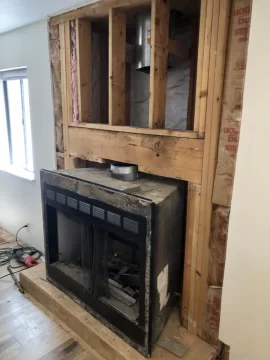
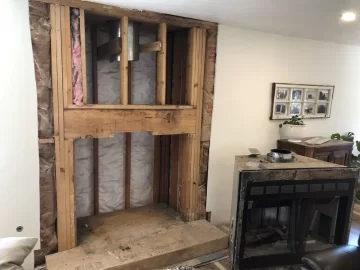
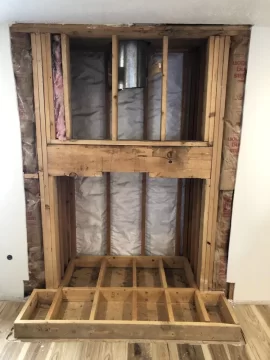
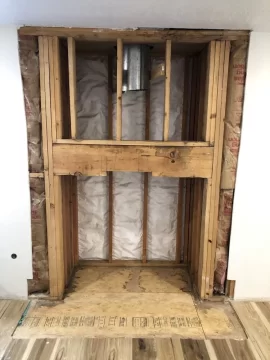
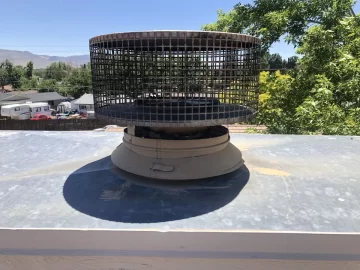
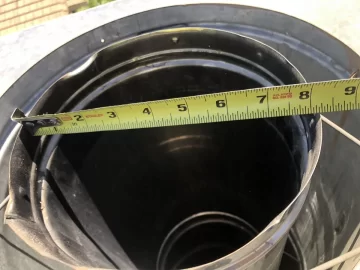
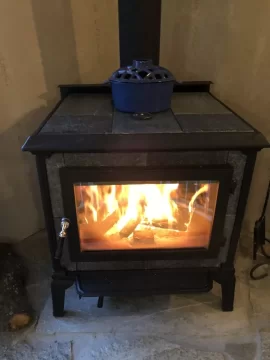
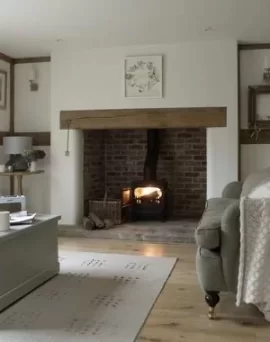
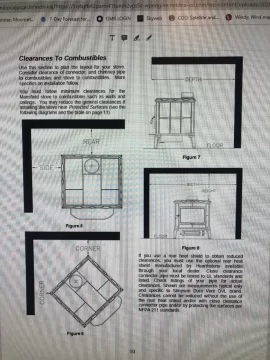
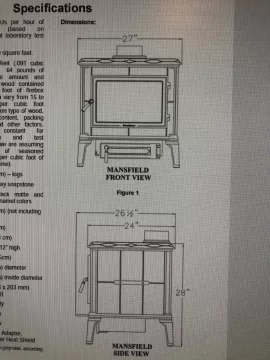
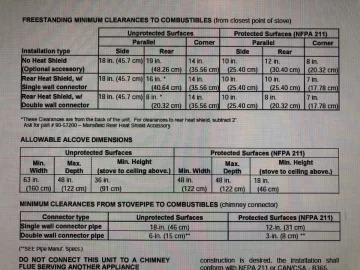
Last edited: