The cinder block was previously knocked out when my inlaws installed a wood stove. I am removing the wood stove and all piping associated with it. I bought a DuraVent 3PVL-KHA vent kit.
I do not own a pellet stove yet, nor is the interior wall finished, but I want to secure the exterior pieces ASAP because the current setup is janky and unsealed. So my immediate question is about the exterior thimble piece, and the broader question is about the rest of the wall cavity.
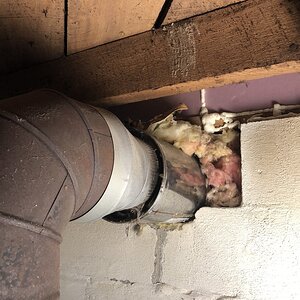
I'm not sure if it's best to create framing inside the hole and somehow attach that inside the cinder blocks, or if I should punt and just attach a board to the exterior and somehow seal it to the sculpted concrete originally slathered on the outside of the cinder blocks (what you're seeing is not stucco.)
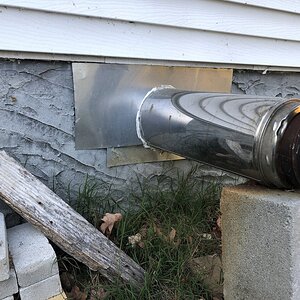
I do not own a pellet stove yet, nor is the interior wall finished, but I want to secure the exterior pieces ASAP because the current setup is janky and unsealed. So my immediate question is about the exterior thimble piece, and the broader question is about the rest of the wall cavity.
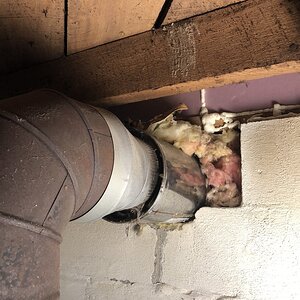
I'm not sure if it's best to create framing inside the hole and somehow attach that inside the cinder blocks, or if I should punt and just attach a board to the exterior and somehow seal it to the sculpted concrete originally slathered on the outside of the cinder blocks (what you're seeing is not stucco.)
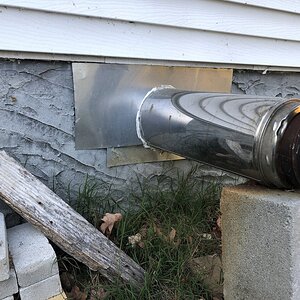