
Madison wood insulation manufacturer to expand distribution in U.S., Canada under new partnership
TimberHP, a division of Belfast-based GO Lab Inc., revived a former Madison Paper Industries mill, and is now partnering with CertainTeed Inc.

Their products:
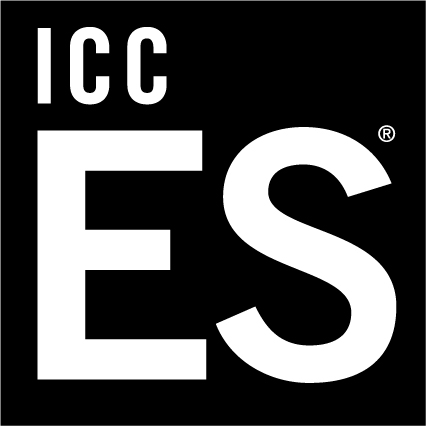
TimberBatt
TimberBatt is a sustainable thermal, acoustical batt insulation that creates calm, climate-controlled spaces.

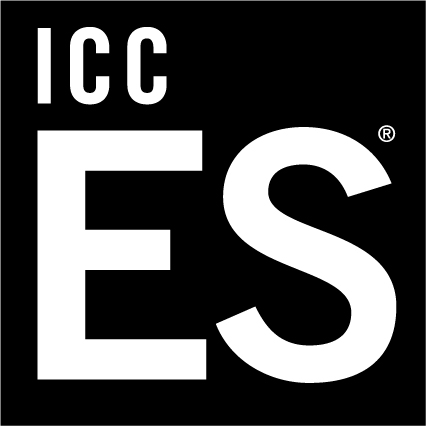
TimberFill
Wood fiber blown-in insulation offers best-in-class performance as attic insulation and cavity wall insulation.
